A University of Wisconsin-Madison professor and a Green Bay company are working together to upscale a new recycling technique that could help keep flexible plastics out of landfills.
The project is still in the early stages — with hopes to open a commercial demonstration facility in Green Bay by 2025 at the earliest.
UW-Madison chemical and biological engineering professor George Huber is helping lead the project. He said a lot of plastics can’t be recycled using traditional methods because they’re composed of a mixture of several types of plastic. Those are typically used for “flexible packaging,” like the plastic wrapped around a string cheese stick or Ziploc bags.
Stay informed on the latest news
Sign up for WPR’s email newsletter.
Wisconsin has a robust packaging industry that employs 43,000 people — 25,000 of which are in flexible packaging — Huber said.
That’s why researchers developed a plastic recycling process called “solvent-targeted recovery and precipitation,” or STRAP, he said. That research was supported by a grant from the U.S. Department of Energy.
“What we do with STRAP is pick a solvent that will selectively dissolve one plastic. We then keep that hot while it’s dissolved, we separate the solvent from the undissolved plastic and then we cool it down,” Huber said. “The plastic precipitates and then you get the pure plastic back that you can use to reuse your original material or remake your original material.”
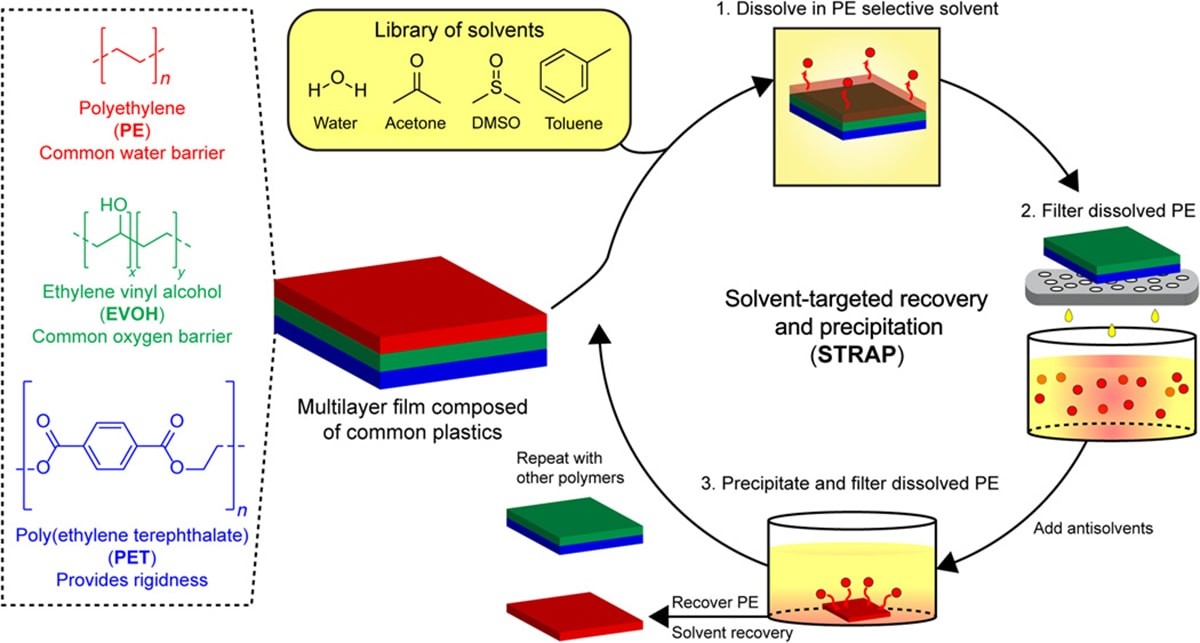
He said efforts to market STRAP have been aided by a partnership with Amcor, a global packaging company based in the Fox Cities. Amcor liked the STRAP technology and asked for samples of the material produced by the process that exceeded what researchers could produce in a lab, Huber said.
That led to another partnership, this time with Michigan Technological University, to design a system that could produce larger volumes of material, Huber said. Through Michigan Tech, Huber came in contact with Green Bay-based Convergen Energy to expand STRAP.
Convergen Energy CEO Ted Hansen said the company already receives materials necessary for STRAP, which it converts into fuel pellets that companies and utilities use to produce steam and electricity.
He said there are four main steps for commercializing, or upscaling, STRAP. First is the lab phase where researchers are working with small quantities of material. Second is a pilot phase where they’re working in a larger-scale lab that’s smaller than a commercial facility. Third is a commercial demonstration unit that’s able to produce large quantities of product at a profitable scale. And fourth is a true commercial facility that’s profitable.
Right now, Hansen said efforts to commercialize STRAP in Wisconsin are still in the lab phase, and Convergen Energy is in discussions to craft a commercial demonstration facility.
“What we can do is put in a commercial demonstration unit, strip out some of these non-recyclable plastics that we’re currently bringing into the facility and you can run them through the STRAP process and now have a recycled polymer that we could sell back to the producers of flexible films and other types of plastics,” he said.
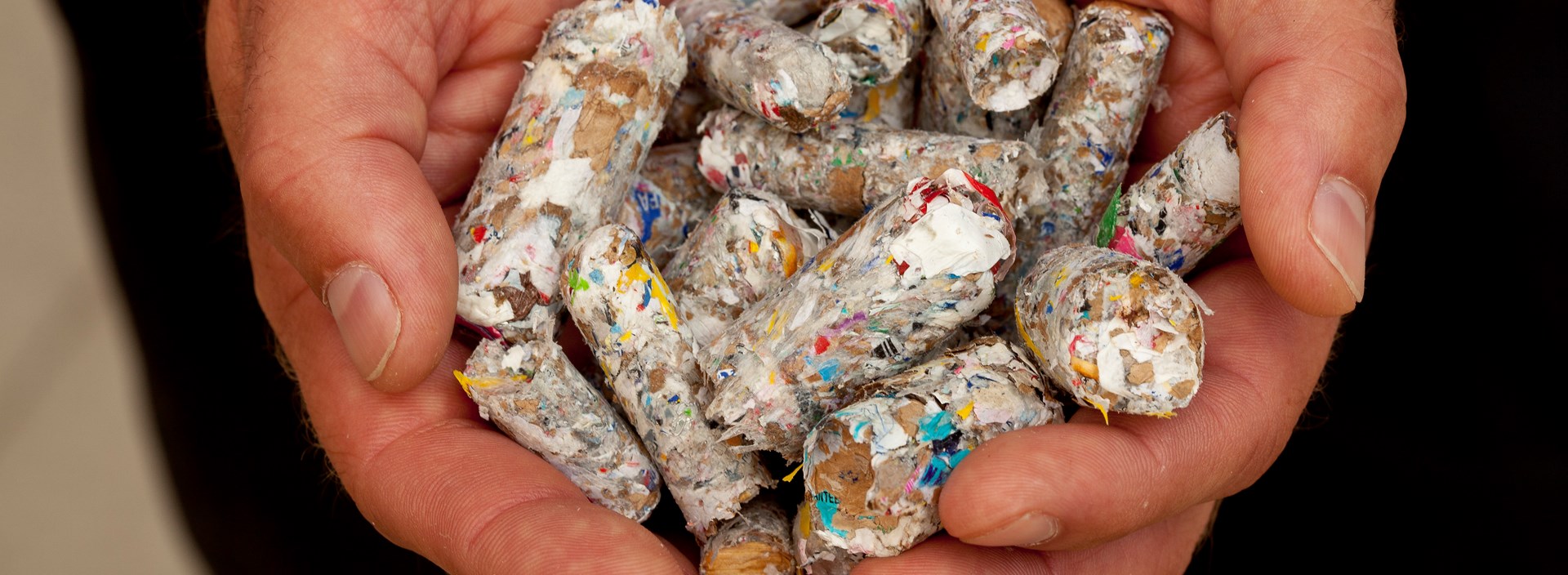
Hansen said the earliest Convergen Energy’s facility would open is 2025, but it could be 2027. The facility would produce 4,000 to 5,000 tons of recycled material per year, and a full-scale commercial operation would double that, he said.
“It really depends on the funding for all these projects, the success of the research, the success of the pilot facility and then, of course, getting financing to install all of this equipment,” he said.
While a commercial demonstration facility may still be several years out, Huber said STRAP’s potential is limitless, especially as Americans are living in the “plastics age” with almost all food products packaged in plastics. Much of that plastic ends up in landfills or is burned, which can have harmful environmental impacts.
“It’s a super important industry for the state of Wisconsin, but we don’t really have technology to recycle most of these plastics that are being produced,” he said. “Wisconsin should also try to become the leader with plastic recycling and how we can more sustainably use the plastic material — I think it’s a critical thing for the plastic industry.”
Wisconsin Public Radio, © Copyright 2025, Board of Regents of the University of Wisconsin System and Wisconsin Educational Communications Board.