Like many luxury apartment buildings, Milwaukee’s Ascent has several special features.
Heated floors. A sky deck. An indoor swimming pool. A pet spa.
But its unique feature is the material the building was constructed with — mass timber.
Stay informed on the latest news
Sign up for WPR’s email newsletter.
Many larger buildings are constructed using concrete and steel, but the 25-story building in downtown Milwaukee was built with mass timber, a newer process that consists of multiple wood panels nailed or glued together.
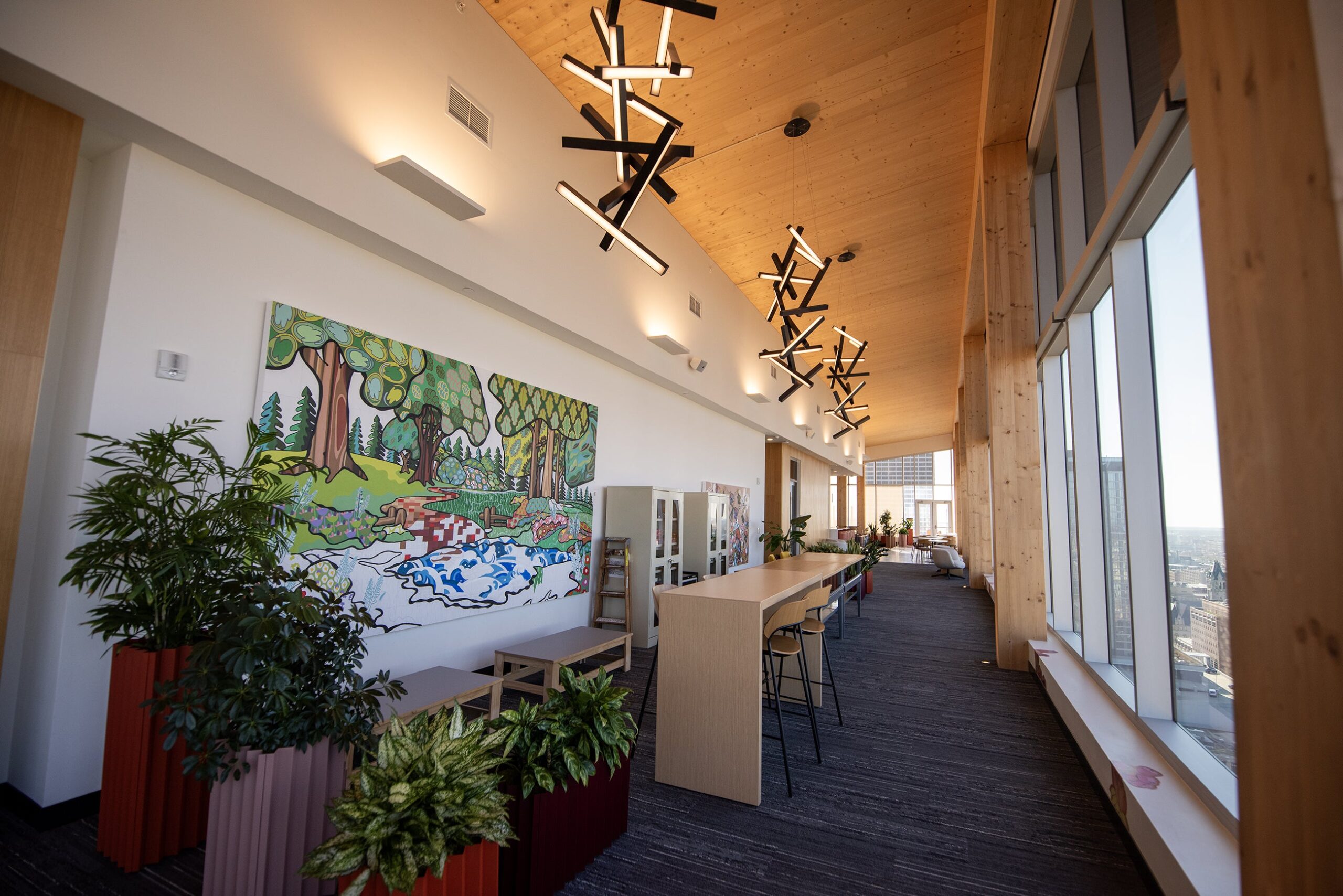
The building, which opened last year, is now officially the tallest mass timber building in the world, standing 284 feet above ground. But from the outside, you’d likely never know it.
Tim Gokhman, the managing director of New Land Enterprises, the developer of the building, said they didn’t set out to achieve that accolade. But in 2017, he read an article about another mass timber project.
He was hooked.
“Once we saw a modern application of mass timber in high rise, right away we understood … this creates a really special built environment that we have never seen before,” Gokhman said. “That was the initial driver, the aesthetics of it.”
Once the building opened last summer, it edged out Norway’s Mjøstårnet, an 18-story mixed-use building in Brumunddal, Norway, as the tallest mass timber project in the world. Ascent has received national and even global attention — it won the CoStar Impact Award this year and Milwaukee Business Journal’s project of the year last year.
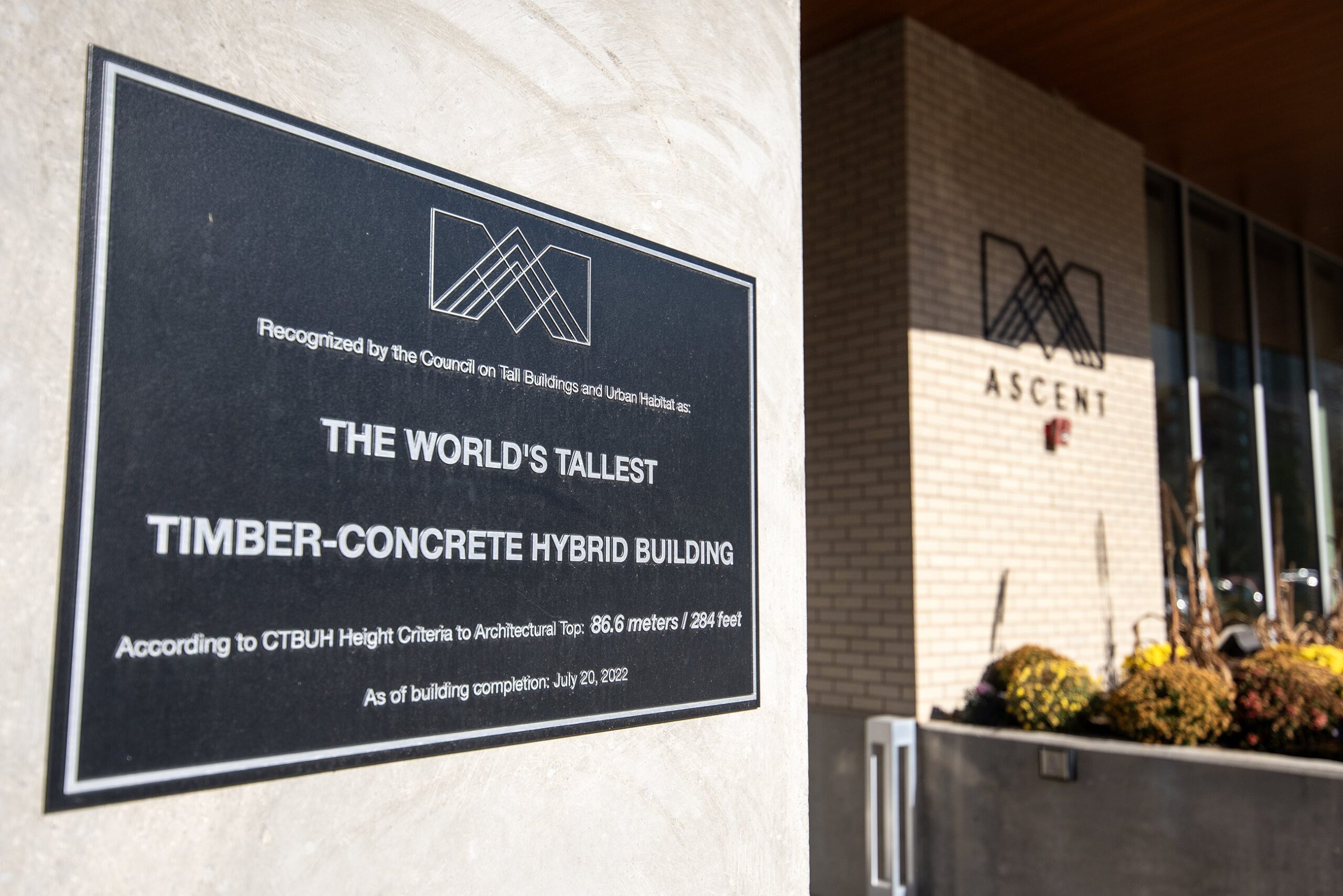
A mass timber building is one that has mass timber — thick and compressed layers of wood — as its primary structural component.
“Mass timber really means that it’s timber in a scale that’s not traditionally used and it’s got these inherent fire-resistant properties that go along with it,” said Paul Crovella, an associate professor at the State University of New York College of Environmental Science and Forestry.
Crovella said mass timber projects have been growing in popularity across North America in the past decade. They’re appealing because of their environmental benefits, economic benefits and health benefits.
The buildings “store tremendous amounts of carbon and reduce the fossil energy needed for construction over alternatives like concrete, steel and aluminum,” according to the U.S. Department of Agriculture Forest Service.
“Oftentimes the impact that the building has when it’s built, in terms of the carbon that’s emitted from the construction materials, is equivalent to the carbon emissions for the next 20, 30, 40 years,” Crovella said of the building’s environmental impact.
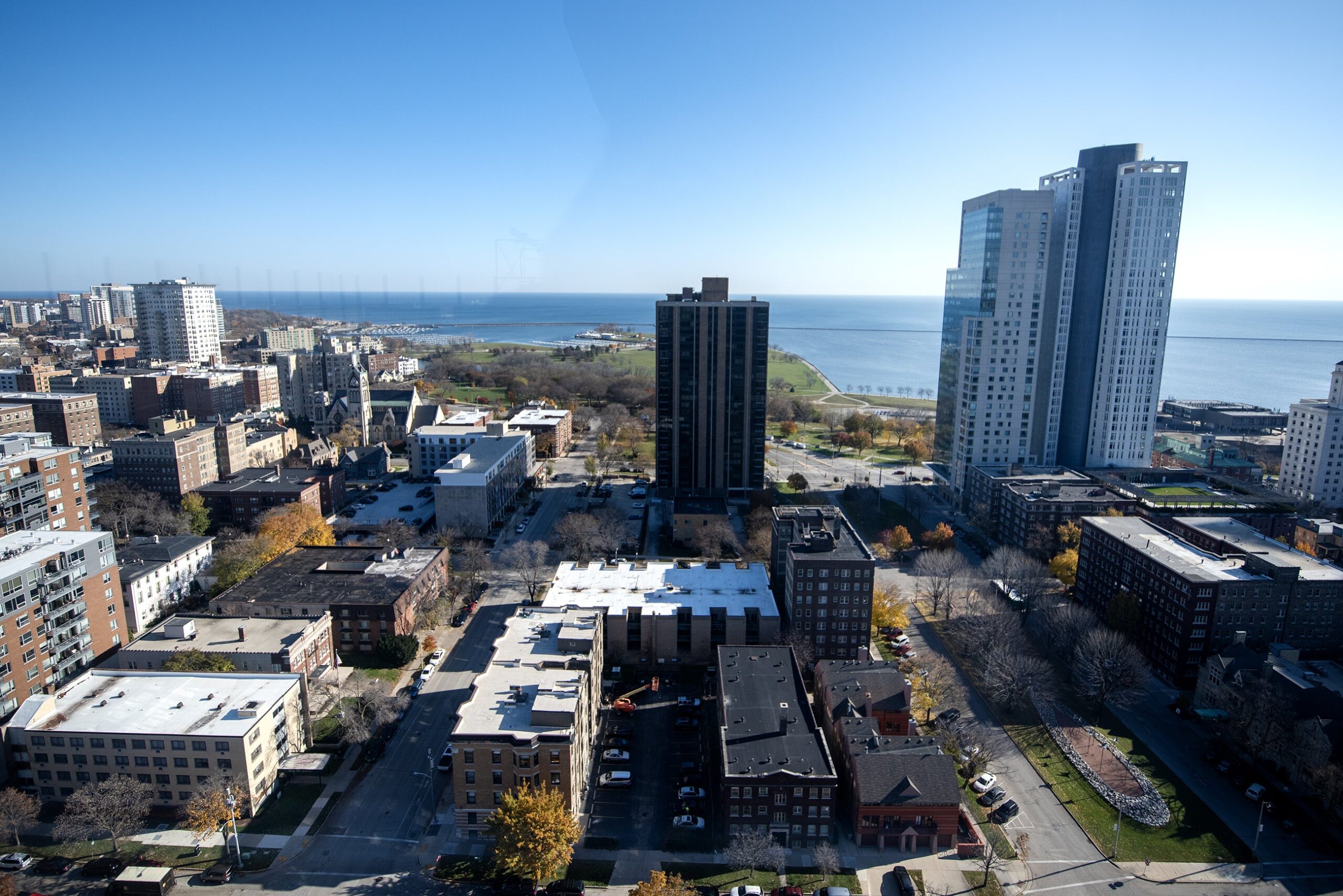
The health benefits of a mass timber project largely have to do with its biophilic elements, or bringing natural elements from the outside to the inside.
“Using wood and exposed wood in our buildings is something that appeals to many folks,” Crovella said.
That was a major motivation for Gokhman as well. Some studies have shown that biophilic design elements can reduce stress, improve mental health and enhance creativity.
“It’s a magical environment, there’s no other way to say it, and it’s not embellishing,” Gokhman said. “We spend so much time inside of our built environments, inside of buildings, and most of our built environments are not biophilic, they don’t feel good, and this one does and that’s very special.”
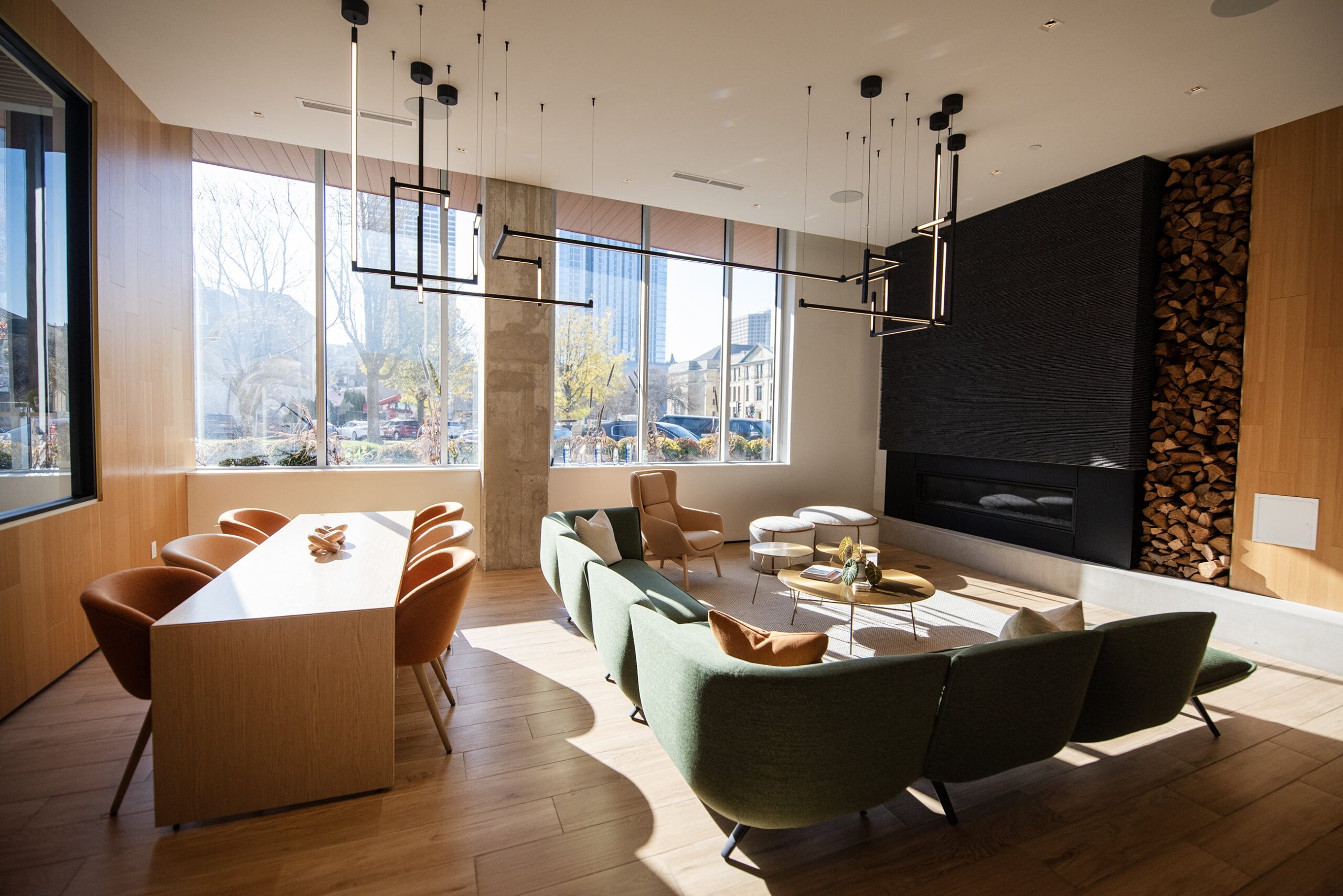
The buildings are also lighter and faster to build. That was the case for Ascent, Gokhman said, as about 12 people — about a quarter of the people they’d have on a normal construction site — assembled the building.
“That’s very, very unusual,” Gokhman said. “And that, we believe, is a better way to build, because fewer people and shorter construction timeframe means less risk, by definition.”
Gokhman said the building process involved the gluing and pressing of dimensional timber together to form massive timber components that could be columns or beams or decks.
“These aren’t two-by-fours, this is not the same material that your house is being built on,” Gokhman said. “This is an engineered wood product.”
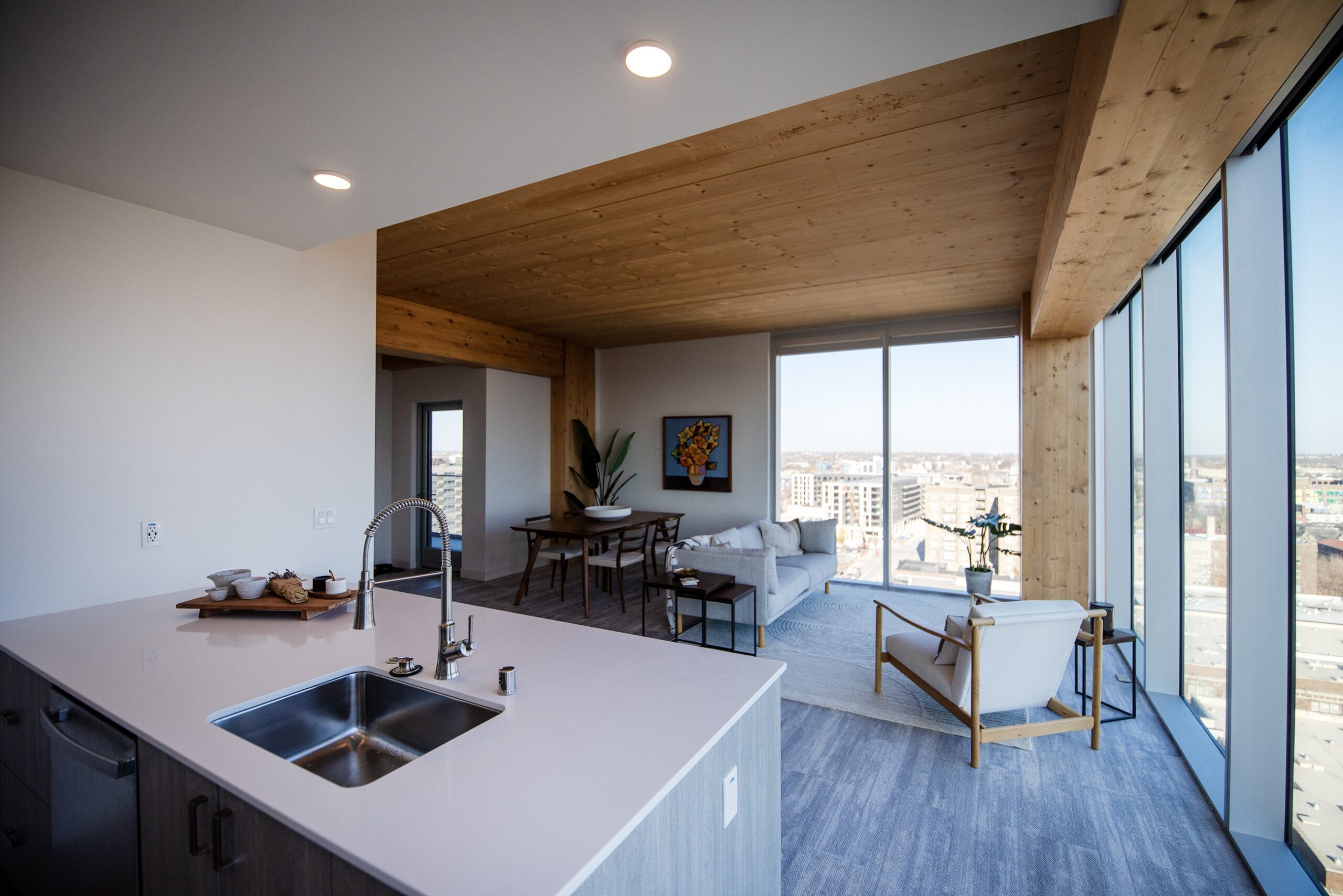
The timber for Ascent is from Austria. It arrived on shipping containers and then traveled by train to Chicago and then on train from Chicago to Milwaukee.
“Once the buildings are enclosed, the cabinets and the floors and everything else, that’s the same, but the initial process is very different,” Gokhman said, adding that the design process was longer than for a normal project.
The project received fire testing through the USDA Wood Innovations program, as a lab conducted fire testing for the glued-laminated timber columns. The lab found that the columns do not lose structural integrity since outer layer charring protects internal layers.
Gokhman said if anyone has ever thrown a log onto a campfire, they know it won’t burn all the way through.
“The reason why it doesn’t burn all the way through is because as wood burns, it forms a char layer on the outside and that char layer oxidizes,” Gokhman said. “And once something oxidize and doesn’t let oxygen through, you can’t have fire without oxygen.”
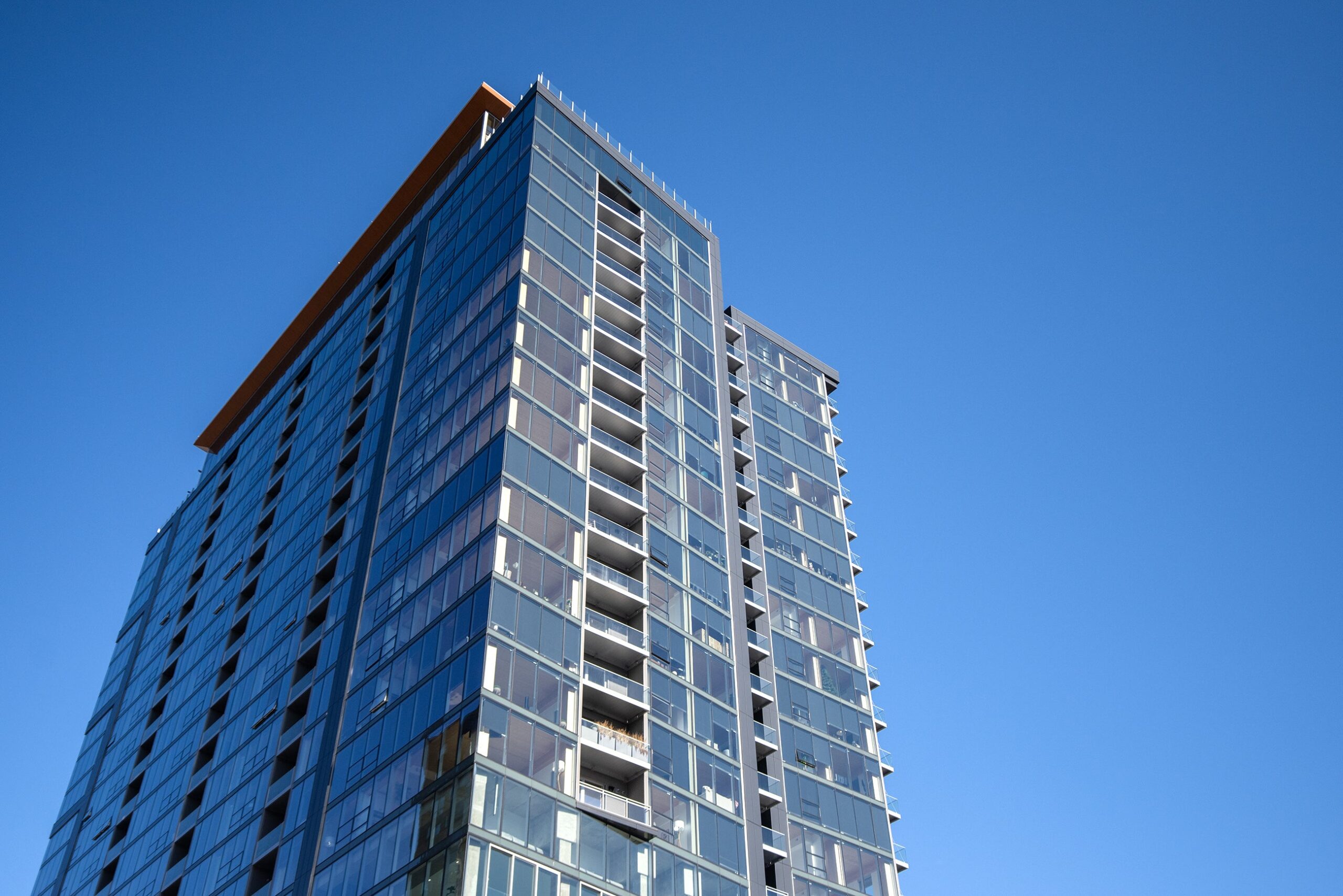
Still, Ascent might not have its claim to fame for much longer. Crovella said there’s an “arms race” of “higher and higher and larger and larger” mass timber projects across the globe, many of them larger apartment buildings or office buildings.
“We really haven’t seen the limit yet for what people have imagined for mass timber in terms of height,” Crovella said.
Wisconsin Public Radio, © Copyright 2025, Board of Regents of the University of Wisconsin System and Wisconsin Educational Communications Board.