Most workers were on break when an explosion rocked the Superior oil refinery, then owned by Husky Energy Inc., four years ago.
In interviews with investigators after the incident, operations manager Brian McCusker recalled hearing two loud blasts that shook the control room of the refinery’s fluid catalytic cracking unit.
“The board operator, one other operator and me were in there. We went to (the) door. I told the other guys to go north out of the unit. I saw asphalt leaking out of the asphalt tank across the road,” said McCusker, according to documents from federal labor regulators obtained by Wisconsin Public Radio. “I tried to find all of my people. Once I knew everyone was okay, I told everyone to just go.”
Stay informed on the latest news
Sign up for WPR’s email newsletter.
The blast knocked workers to the ground, injuring 36 refinery workers and contractors. Two workers suffered serious injuries including a punctured lung and spinal fractures while others walked away with minor cuts and bruises.
Debris from the explosion struck a nearby tank and asphalt spilled into the refinery, catching fire and creating a large plume of black smoke that could be seen for miles. Many of the city’s 27,000 residents were forced to evacuate due to the smoke and fears that a tank containing the highly toxic chemical hydrogen fluoride may be compromised. Parents waited in bumper-to-bumper traffic to pick up their kids who were bussed to a nearby evacuation site. While no chemical release occurred, evacuees stayed overnight in Duluth at hotels and a local convention center until authorities lifted the evacuation order the next morning.
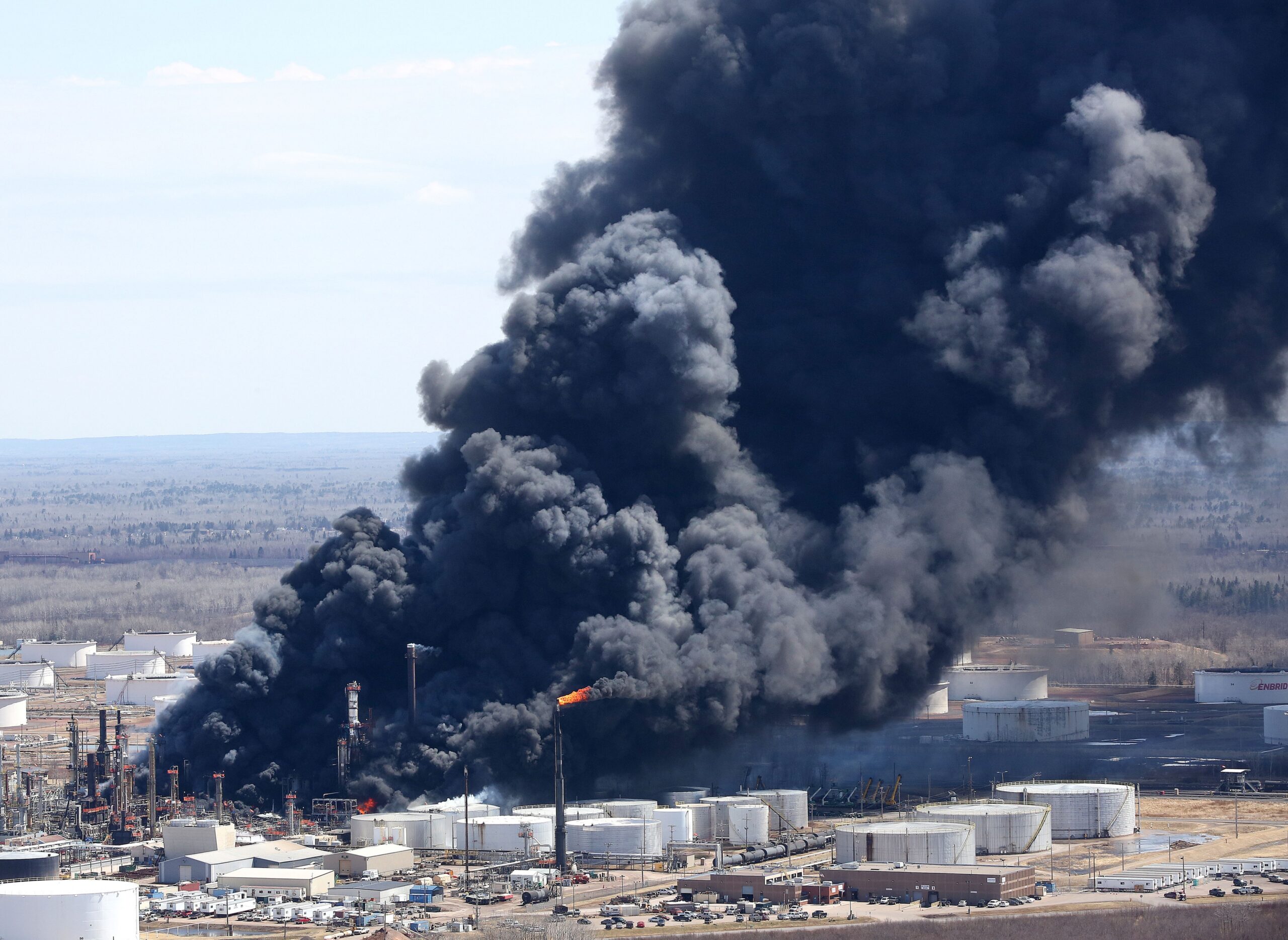
The Occupational Safety and Health Administration, or OSHA, previously fined the refinery more than $83,000 for failing to take steps to protect workers and prevent the incident. The company reached a nearly $70,000 settlement with the agency in 2018.
Nearly 1,300 pages of documents from OSHA obtained by WPR shed new light on what refinery officials knew in the days leading up to the explosion. The documents also indicate the company was aware years earlier of issues with the very equipment investigators believe caused the explosion.
These include problems with a critical valve malfunctioning days before the explosion and documented erosion on that key piece of equipment dating back to 2008.
Calgary-based Cenovus Energy Inc., the refinery’s new owner, said officials have since taken steps to improve safety in their operations. Those actions will play a vital role in mitigating risks as the refinery will continue using hydrogen fluoride — which can be hazardous to human health if released — as part of its refining process to make gasoline.
Refinery knew about erosion on key valve, other malfunctions prior to explosion
The refinery is located just a few miles from Lake Superior, and its tanks and towers are clearly visible from Duluth’s hillside. Built in 1950, it has operated in the city for more than 70 years under several owners, and typically employs around 200 workers year-round.
In 2017, Husky Energy bought the refinery from Calumet Specialty Products in a $435 million deal. Calumet bought the facility in 2011 from Murphy Oil, which had operated the refinery since 1958. The facility processes heavy and light crude oil from Canada and North Dakota’s Bakken oil fields. It produces gasoline and diesel for the region, as well as asphalt, a byproduct of the refining process. Last year, Cenovus Energy became the new owner of the refinery after it bought Husky Energy in a roughly $5 billion deal.
When the explosion happened on April 26, 2018, the refinery was shutting down its fluid catalytic cracking unit as it prepared for a five-week “turnaround,” or a routine break in production conducted every five years by the refinery to perform maintenance. The unit uses heat and a sand-like catalyst to crack or break apart large hydrocarbons of crude oil into smaller molecules to make gasoline and other products.
In August 2018, the U.S. Chemical Safety Board, or CSB, said internal wear on the spent catalyst slide valve likely caused the explosion by failing to separate air and hydrocarbons between the reactor and regenerator as part of the fluid catalytic cracking unit.
Even though the valve was closed, air was able to leak backwards through the eroded valve and into equipment downstream that contained hydrocarbons. The combination created a flammable mixture that eventually ignited, causing the explosion. A final report on the CSB’s findings has yet to be released, and the board said during a meeting Thursday it now expects to wrap up its investigation next year.
Documents from OSHA show the refinery was aware of erosion on that valve during past turnarounds for at least a decade, according to a 2018 report from OSHA’s Health Response Team.
“According to interviews and records, holes were found in the spent slide valve on two past turnarounds (April 2008 and April 2013), and those interviewed indicated that they were aware that this valve could leak because of catalyst erosion on the leading edge of the valve gate and seat ring,” the report states.
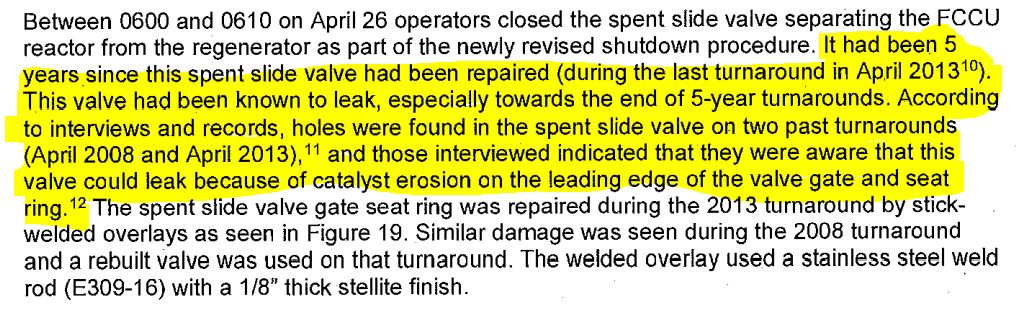
Despite that knowledge, the refinery continued to use the valve and maintain its same schedule for repair and replacement every five years, according to OSHA documents. The agency found the refinery should have inspected the valve more frequently and possibly moved up the timeline for replacement. The refinery also failed to follow its own policy and procedure for ensuring mechanical integrity of equipment, according to OSHA.
Mark Wingard, a former investigator for the Chemical Safety Board, said during a 2018 board meeting in Superior that it’s normal for slide valves to erode over time, and the valve “might not be the best design for serving to stop to create a barrier during a shutdown.”
Three years prior to the explosion, the CSB found erosion of the spent catalyst slide valve had caused a similar explosion at a refinery in Torrance, California, then owned by ExxonMobil. It’s unclear whether refinery officials in Superior were aware of the incident, according to OSHA documents.
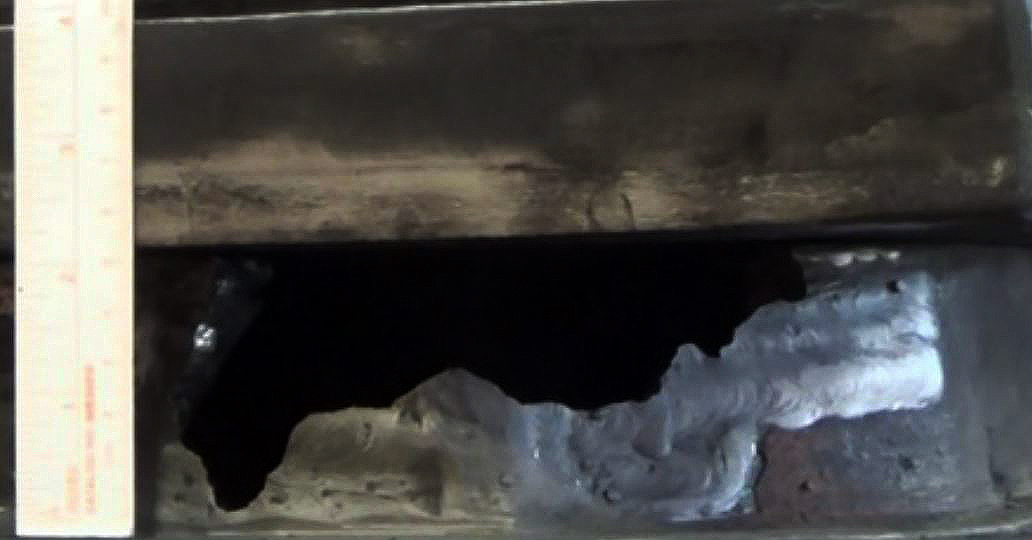
Furthermore, the CSB has previously said conditions existed at times on the morning of April 26, 2018, that could have allowed air to flow backward through the eroded valve. An instrument that measures the difference in pressure above the valve from pressure in the regenerator below displayed a reading that showed air could have flowed backward into downstream equipment for 10 percent of the time that morning.
OSHA’s investigation noted it was the board operator’s first turnaround, and the board operator wasn’t monitoring the difference in pressure related to the spent slide valve. Furthermore, there was no step in the refinery’s shutdown procedure indicating that level was important to monitor to prevent air from flowing backward.
Workers interviewed by OSHA also reported hearing two booms in the final hours before the explosion that morning. After the second boom, the agency’s inspection team said they were surprised the shutdown continued after a limited search revealed no exact cause.
In the week leading up to the explosion, workers had also noted in operator logs that the valve was malfunctioning. Problems with the valve resulted in the shutdown of the refinery’s Electrostatic Precipitator, a pollution control device, on April 19 and April 22.

“Operators interviewed noted they had put in several work orders for the malfunctioning spent slide valve; however, only one work order was provided from 2017 that showed it was having issues,” the agency found.
Refinery employees told OSHA it was common for the valve to experience sticking or have debris that would need to be cleared manually near shutdowns. The refinery didn’t investigate those issues or take any interim measures to address the potential for the valve to fail, the agency found.
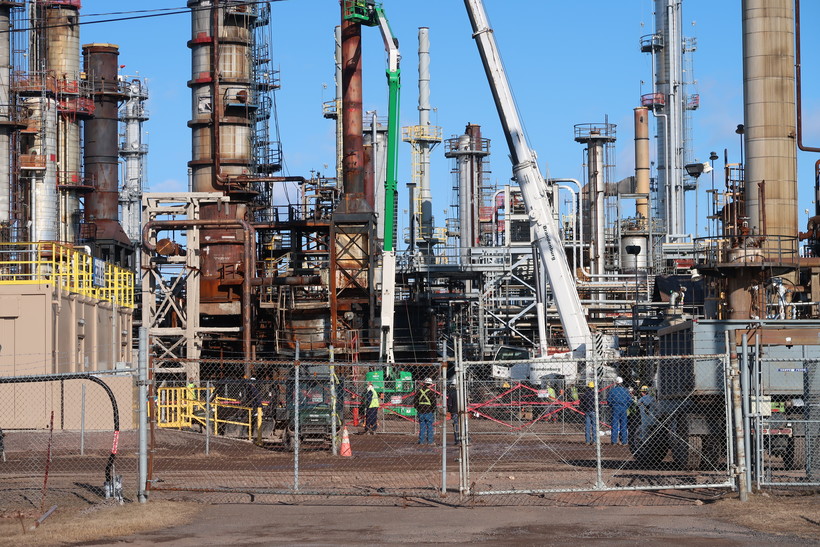
Workers’ lawsuit seeking damages from the explosion is ongoing
The explosion prompted multiple lawsuits against the refinery. Four years after the blast, Husky reached a roughly $1 million settlement agreement in June last year as part of a federal class-action lawsuit brought by residents for lost wages and lodging due to the evacuation. The company also reached an amended settlement with the state and federal government to offset emissions from the explosion.
Nine contractors injured by the explosion are suing the refinery for more than $10,000 in medical bills and lost wages. Attorney Kyle Findley, who represents the contractors, said investigations by the Chemical Safety Board and other entities show things had been going wrong at the refinery for a long time.
“The bottom line is, with the information that is out there and is available, that this was 100 percent preventable.” said Findley. “It was something that should not have happened. It was something that should never happen in any type of situation.”
Husky, which does business in Wisconsin as Superior Refining Company, has previously sought to dismiss the case, arguing that the contracted turnaround work at the refinery was inherently dangerous and that the company hadn’t been negligent.
Court documents say the contractors were thrown to the ground by the blast and showered with debris and shrapnel from the explosion. Findley said his clients have suffered anxiety, post-traumatic stress disorder and physical injuries that have required surgeries and jeopardized their ability to return to work.
He said they’re seeking whatever a jury decides is fair in compensation for the pain and suffering they’ve experienced.
Refinery was using a repaired valve
The spent slide valve that had been malfunctioning in the days leading up to the explosion had previously been repaired during the last turnaround in 2013, according to OSHA’s Health Response Team.
The refinery used Oklahoma-based contractor Houston Services to repair and inspect the slide valve in 2008 and 2013, noting severe erosion as part of inspection reports provided to the refinery’s maintenance manager. Even so, OSHA’s team found no documented inspections of repairs by the refinery’s inspectors nor any evidence of preventive maintenance work on the valve from 2008 until the explosion.
“Interviews of Superior Refining Company employees and managers confirmed that inspections and (preventive maintenance work) had not been done,” the team reported. “Further, there was no indication that the spent slide valve was evaluated on either occasion for continued fitness-for-service as a result of the damage and the repairs.”
Ken Rikkola, the refinery’s maintenance manager, told OSHA that welding brought the valve back to new condition. He said weld overlays on the valve were inspected and tested, voicing concerns that a newer valve may not be as reliable. WPR reached out to Rikkola, who didn’t return a request for comment.
Gary Johnston, the refinery’s chief inspector, told OSHA he didn’t “get heavily involved” with the slide valves. Johnston declined WPR’s request for comment, citing ongoing litigation.
In a redacted Nov. 8, 2018 email, a member of the OSHA Health Response Team informed the agency’s assistant area director Ruth “Mitzy” Wright that the repair to the spent catalyst slide valve “was unsatisfactory with poor weld overlays.”
“We hope that Superior takes a hard look at any weld overlay repairs on any other slide valves including the ones in storage,” the email states.
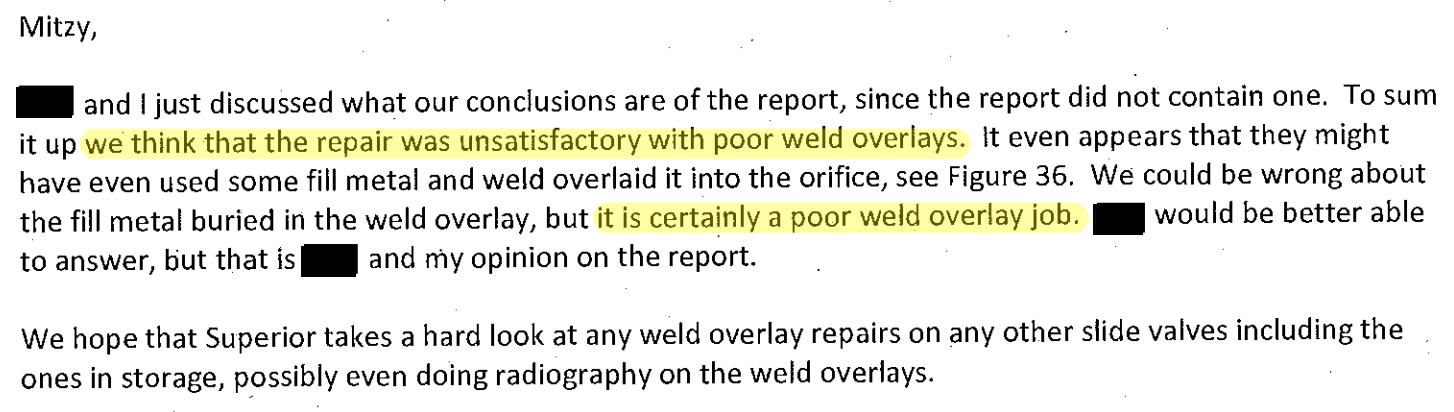
WPR reached out to Houston Services, which did not return a request for comment.
The spent catalyst slide valve was not the only piece of equipment that had issues, according to OSHA. Two vessels that exploded — the primary and sponge absorbers — had shells made of carbon-silicon steels that were installed in 1961. The standards for those metals were withdrawn by the late 1960s. The primary absorber was constructed of steel where known failures of the metal occurred due to brittle fracture or sudden cracking under stress.
Even so, OSHA found no signs the refinery assessed whether that vessel was susceptible to brittle fracture, and testing indicated both failed absorbers had metal embrittlement.
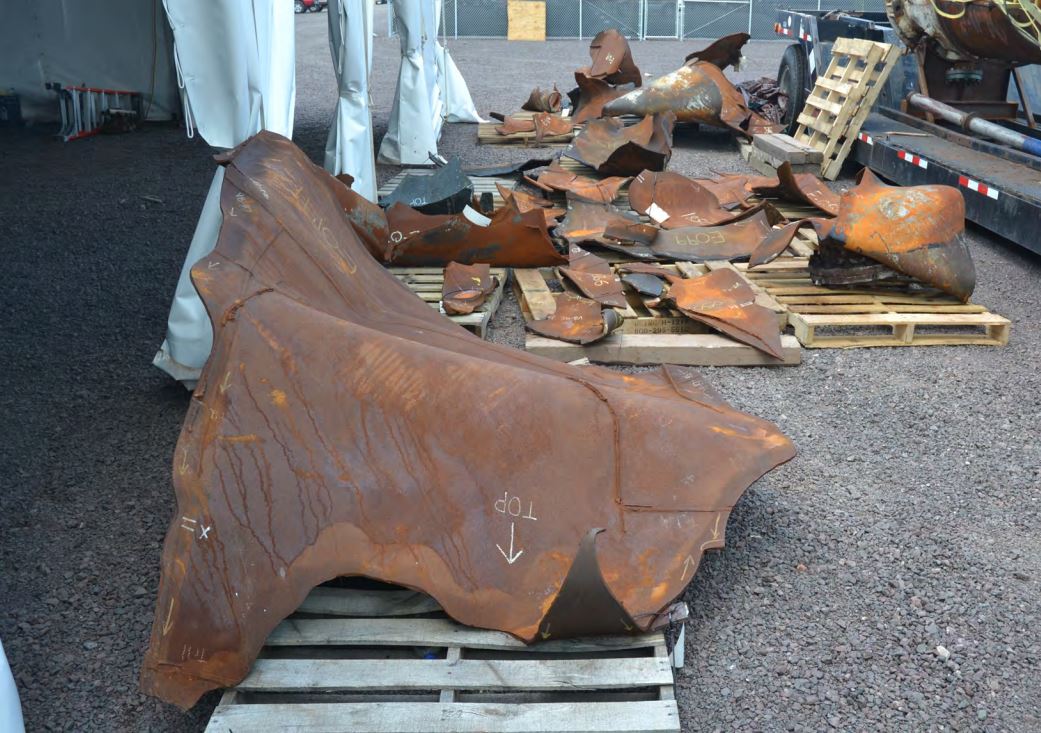
In a statement, Cenovus said the refinery is taking steps consistent with OSHA’s recommendations to verify the condition and operability of equipment and control systems.
“The facility is being rebuilt with state-of-the-art equipment, incorporating advances in technology and efficiencies made across the refining industry,” the company said.
Cenovus said that includes new crude and fluid catalytic cracking units that have new state-of-the-art slide valves with advanced instrumentation that will allow operations and engineering staff to monitor their performance. The company said it has resolved all of OSHA’s recommended abatement actions.
The company added that process hazard analyses have been completed for new and unaffected areas of the refinery. OSHA’s inspection team found none of those reviews addressed erosion of the slide valve or the potential for air to enter the system during startups or shutdowns prior to the explosion.
OSHA said in a statement that the agency discussed concerns with the refinery during the planning phase of rebuilding the facility, adding it reserves the right to conduct follow-up inspections.
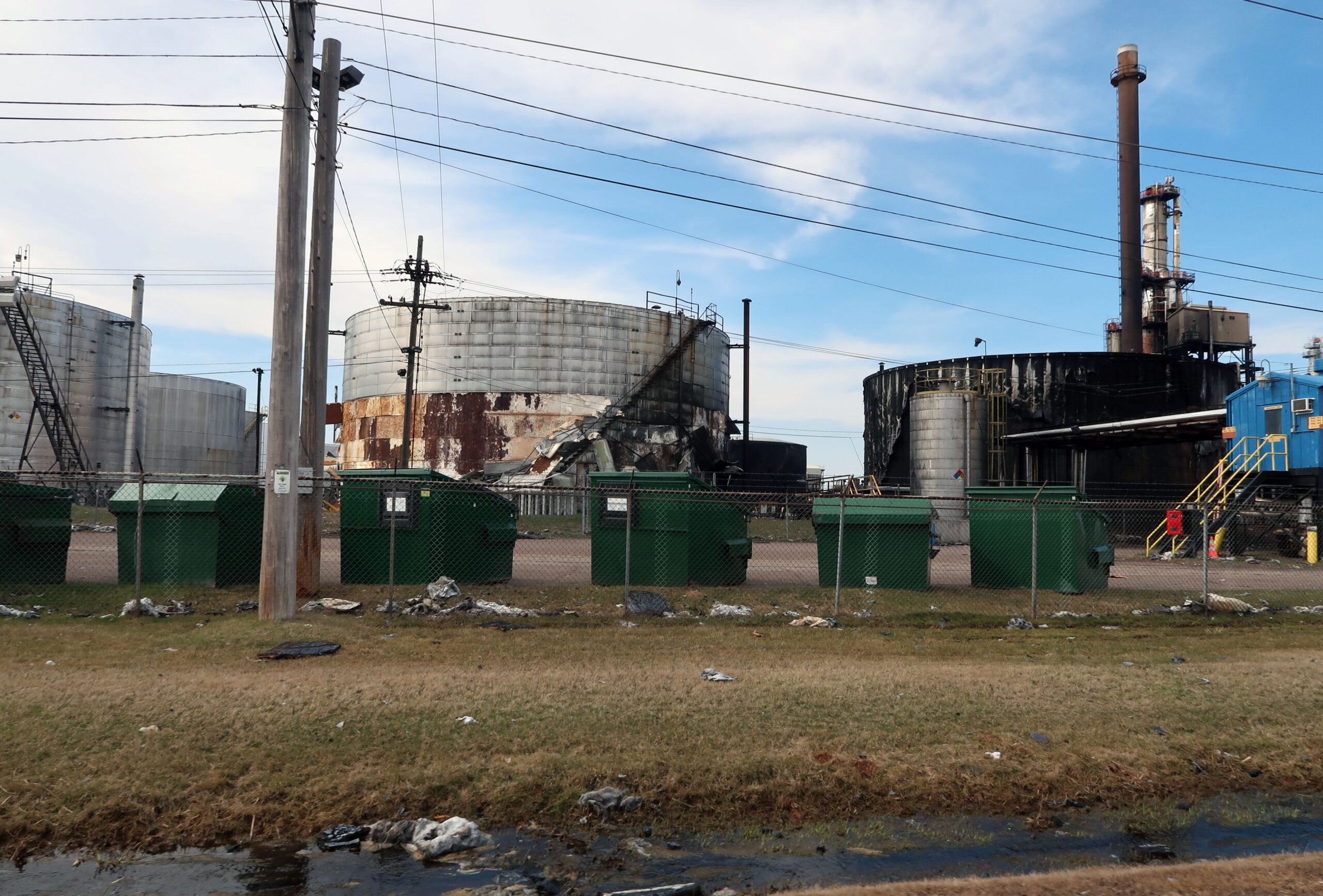
Former OSHA official says issues revealed are common at refineries nationwide
The problems uncovered at the Superior facility are not uncommon at refineries nationwide, according to a former top OSHA official. Many refineries, including the Superior refinery, were built around 60 or 70 years ago.
Jordan Barab, who served eight years as deputy assistant secretary for OSHA under former President Barack Obama, said he often saw written procedures and training that didn’t reflect actual changes that had been made to equipment at refineries. Because refinery disasters don’t happen often, Barab said they’re often characterized as “low frequency but high impact” events.
“From the employers’ perspective, why invest money in something that probably isn’t going to happen?” said Barab. “Especially if you know that money can be better spent — or better from their perspective — better spent increasing their profits. Obviously, rewriting procedures and retraining workers and all that kind of stuff is not something that directly leads to profit.”
The refinery had rewritten its operating procedure for shutting down the fluid catalytic cracking unit a day before the explosion, but OSHA’s inspection team found operators in the unit’s control room were following the new procedure without adequate training. Most operators received the revised instructions on the morning of the explosion.
Employees indicated the new procedure was confusing with new and deleted steps. The agency found the refinery didn’t provide clear instructions to address consequences of deviating from the instructions and how to correct situations like the reverse flow of air that investigators believe caused the explosion.
Cenovus said “virtually all” refinery operating procedures have been rewritten since the explosion. The company also said it’s now using an electronic management of change system, a process that seeks to ensure environmental, health and safety risks are evaluated prior to making significant changes.
“We have developed new training materials which combine classroom and field training, along with directed training by subject-matter experts, and training simulators which will match control room equipment, allowing tailored training across a range of operating conditions,” the company said.
Employers must document how they’ve addressed violations, but Barab noted OSHA doesn’t have the resources to inspect every workplace after issuing citations. Under the Trump administration, the number of OSHA inspectors fell to levels that would take the agency more than 165 years to investigate every workplace just once, according to the National Employment Law Project.
Barab said robust involvement from workers is important to improve safety. He noted workers who belong to a union tend to have better knowledge of safety standards than their non-unionized peers and gain more workplace protections through actions like filing complaints.
“That presumes, of course, that the workers in the plant have been trained about the process safety management standard and understand what the requirements are and understand what their rights are,” said Barab.
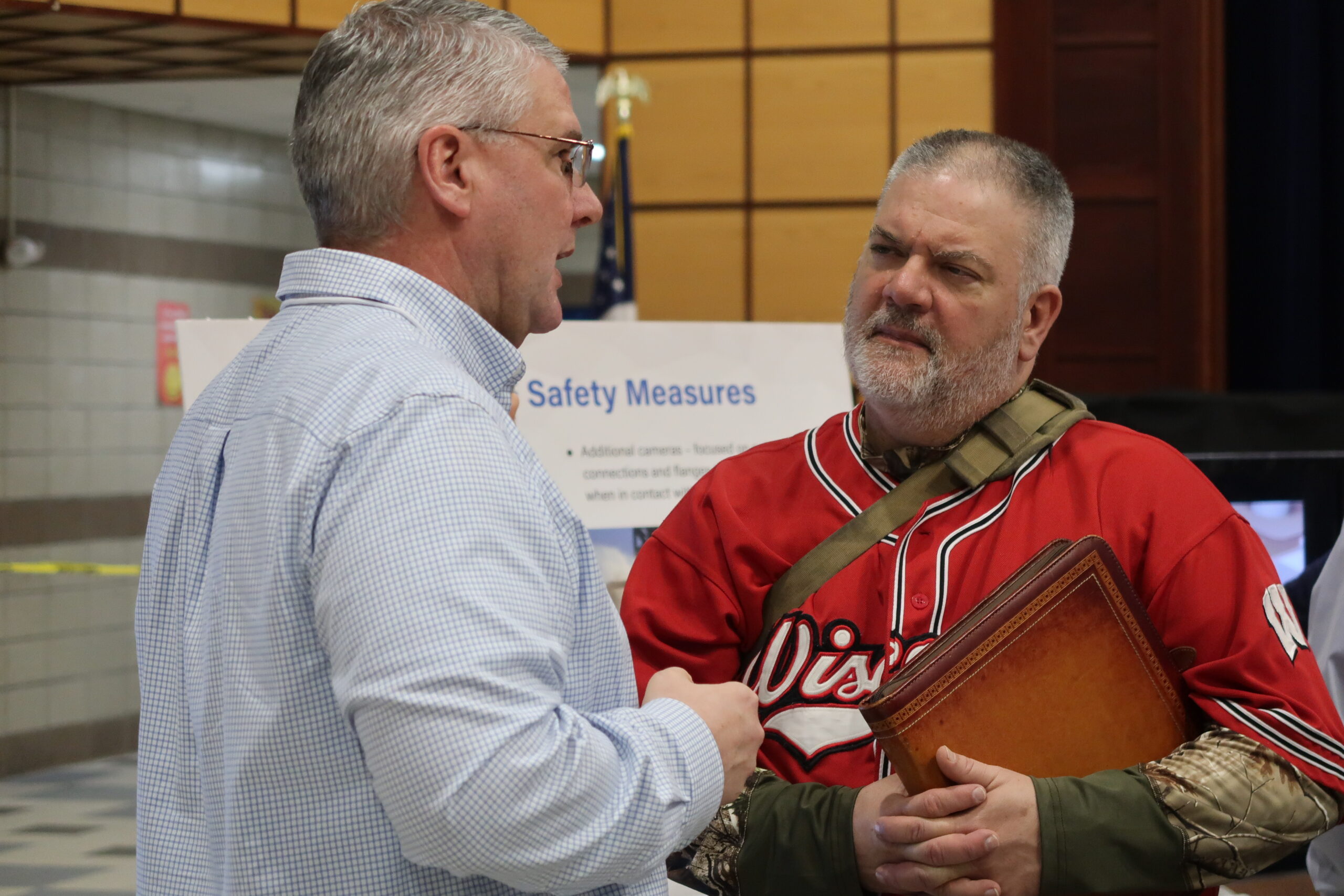
Danielle Kaeding/WPR
Despite OSHA’s investigation, which included interviews with more than a dozen refinery workers, contractors and union representatives, few have spoken publicly about the explosion and its aftermath for them.
Eric Mathews, a boilermaker for Wales, Wisconsin-based contractor CTS, Inc., who was working at the refinery on the day of the explosion, told the Duluth News Tribune that day that he heard “a big sonic boom” while he was on break about 200 yards away.
“I was running and then the debris started falling out of the air … I stopped under a pipe rack then waited for the debris to stop falling,” Mathews told the Duluth newspaper.
He said it was lucky that most contractors were in blast-proof buildings when the explosion happened.
WPR reached out to nine contract companies that were at the refinery on the day of the incident, according to OSHA records. Most didn’t respond to requests for comment, while others declined to speak, referring questions to local union representatives. WPR reached out to four local union representatives who either didn’t respond or declined requests for comment with one labor official citing ongoing litigation.
In an April 27 conference call, Cenovus CEO Alex Pourbaix said the cost of rebuilding the refinery has tripled from an initial projected cost of $400 million to $1.2 billion due to COVID-19 supply chain issues and inflation. Pourbaix said he expects those costs will be covered entirely by insurance. The company said the refinery remains on track to resume normal operations in the first few months of 2023.
The lawsuit filed by contractors who were injured that day is still pending, and Findley said his clients want to see the refining industry invest in the best practices and technology at facilities nationwide to keep workers safe.
“We don’t want to see workers being put at risk. We don’t want to see communities being put at risk,” he said. “If these refineries are going to come and operate and make the money that they do, they need to also likewise spend that money to make sure that they’re protected, make sure the community is protected, and make sure that corners are not cut so things like this don’t happen.”
Wisconsin Public Radio, © Copyright 2025, Board of Regents of the University of Wisconsin System and Wisconsin Educational Communications Board.